In industrial and mobile machinery, hydraulic hoses play a critical role in ensuring smooth operation and efficiency. However, premature hose failures can lead to costly downtime, reduced productivity, and even safety hazards. To maximize hose lifespan and prevent unexpected failures, it is essential to focus on proper selection, installation, and maintenance.
Choosing the Right Hose for the Application
Selecting the appropriate hose for the operating conditions is the first step in ensuring longevity. Continental’s application engineers work closely with customers to assess factors such as pressure, temperature, media compatibility, and environmental conditions.
"Our team takes the time to understand your operating conditions so we can recommend the right hose construction, reinforcement, and cover materials for the job,” says Alex Ng, Continental’s Application Engineer for their Customer Engineered Solutions division. “It’s not just about picking a hose—it’s about optimizing performance and durability. We also help with installation, routing, and maintenance tips to keep your equipment running longer and minimize downtime."
Various factors must be considered when choosing the right hose for your application, including:
Safety Factor: Ensure hoses have an adequate safety margin beyond the working pressure. This precaution helps prevent bursts and failures under extreme conditions.
- Rubber vs. Thermoplastic Hose: Rubber hoses offer flexibility and durability, while thermoplastic hoses are lighter and provide better resistance to certain chemicals and extreme temperatures. Choosing the right material depends on the application.
- Abrasion Resistance: Hoses are often exposed to rough surfaces, sharp edges, and constant movement. Opting for hoses with enhanced abrasion-resistant covers can extend service life. Continental’s XLife™ XR16SC is a superior performer in this category.
- Temperature Tolerance: Operating temperatures – both internal (fluid) and external (environmental) – must be considered. Selecting a hose with appropriate temperature resistance prevents premature degradation. With temperature ranges from -70 °F to 212 °F, Continental has a range of high temp & low-temp hoses to meet customer temperature variation needs.
- Continental has a range of high temp & low-temp hoses to meet customer temperature variation needs.
Proper Selection of Hose Fittings
Even the most durable hose can fail if paired with an incompatible fitting. Proper selection of hose connections is crucial.
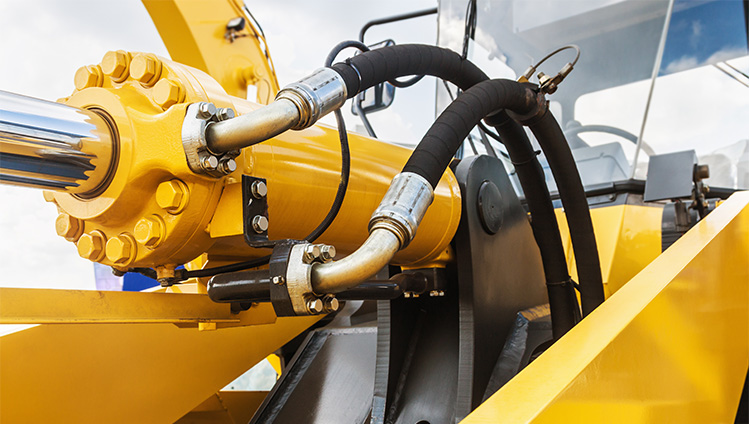
- Fluid and Pressure Requirements: Ensure the hose and fittings are rated for the operating fluid and pressure levels.
- Fitting Material: The material must be compatible with the environment and fluid type. Special coatings or heat-resistant materials may be necessary for extreme conditions.
- Correct Size: Improperly sized fittings can lead to leaks, restricted flow, and pressure drops, all of which reduce system efficiency and increase wear on components.
Optimizing Hose Routing for Longevity
Incorrect routing can significantly shorten a hose’s lifespan. Poorly routed hoses are more likely to experience excessive wear, stress, and failure. Best practices include:
- Minimizing Bending: Excessive bending can weaken the hose structure and lead to cracks or leaks. Routing should follow natural flow paths with minimal stress points.
- Avoiding Kinks: Kinking restricts fluid flow and increases pressure in unintended areas, causing damage over time.
- Reducing Abrasion Risks: Hoses should be kept away from sharp or moving components that can rub against them, leading to cover wear and exposure of reinforcement layers.
- Preventing Crushing: Hoses should be protected from being stepped on, pinched, or compressed under heavy machinery to maintain their internal integrity.
Regular Inspection and Preventive Maintenance
Routine inspections can identify potential failures before they cause serious issues. A maintenance schedule should include.
- Checking for Cover Wear: Look for cracks, cuts, or signs of abrasion. Damaged covers can expose reinforcement layers, leading to failure.
- Inspecting for Leaks: Even small leaks can indicate underlying issues. Address leaks immediately to prevent escalation.
- Assessing Other Damages: Swelling, blistering, or deformation could signal internal hose degradation or chemical incompatibility.
Proper Assembly of Hydraulic Hoses
The final key to maximizing hose life is ensuring correct assembly procedures. Hoses should be cut cleanly, fittings should be crimped to manufacturer specifications, and proper flushing should be conducted to remove contaminants before installation.
By following these best practices, operators can extend the lifespan of hydraulic hoses, reduce unplanned downtime, and improve overall machine efficiency. A proactive approach to hose selection, routing, and maintenance will ultimately lead to cost savings and safer operations.
Ready to make a Continental shift?
Let’s power your hydraulics forward – Contact us today!