Hydrogen (H2) has a lot of potential – but also high requirements. Continental is accompanying the development from its origins to the fuel cell.
When two fit together, they never let go of each other, go through thick and thin, and are stronger as one. Many species in the animal world – penguins, orcas or tapirs – are just as convinced of this concept as many human couples. Even among the smallest elements in our world, which can only be seen under a microscope, there are many pairs: oxygen, nitrogen, fluorine or iodine, for example, are only stable when they join forces with a second of their kind – and can then develop their full potential. The same applies to hydrogen – and that makes H2 a beacon of hope for the mobility of the future wherever high weight, long charging cycles and short ranges of electric batteries are a problem.
However, there is still a long way to go before hydrogen can power trucks, buses or excavators on a large scale, and all those involved – including the materials experts at Continental – still have to pave the way. We wanted to know more about this element, its capabilities, needs and goals, and to this end, we accompanied a hydrogen couple on its journey from creation to the fuel cell.
In the beginning was water
Why hydrogen? Although there is enough of the first element in the periodic table on our planet, it is usually bound in organic form, for example together with oxygen – H2O. However, in order to use pure hydrogen, it must first be released or produced using energy. Is this worthwhile at all? Yes, because with a gravimetric energy density of 120 kJ/g, it is a much better energy store than lithium-ion batteries, for example – and can thus achieve greater ranges, as required in heavy-duty transport, for example.
The most promising future technology for the starting point of our hydrogen journey is electrolysis, in which water is split into hydrogen and oxygen using electricity. The advantage over other technologies is that no harmful emissions such as CO2 are produced – as long as the electricity used comes from renewable sources. That is why this hydrogen is also referred to as "green”.
This is where our two hydrogen atoms met and joined forces as permanent companions on their trip toward the fuel cell. Because pure hydrogen may be a colorless and odorless gas, but is not harmless to handle, the rest of the route must fulfill a number of important properties to ensure that the two arrive safely at their destination. These include, for example, the pressure resistance of lines, seals and tanks.
Hydrogen is transported at up to 700 bar, depending on its state of aggregation – a sealing ring or hose has to be able to withstand that pressure. For it to do so, extensive basic research is being carried out in our competence centers for hydrogen and fuel-cell technology to achieve the necessary properties of the plastics and rubbers. Among other things, there are already hydrogen bunker hoses in Continental's product portfolio that can safely transport compressed H2 under pressures of up to 345 bar.
The journey is the H2 reward
Having just come into being, our dynamic duo must make an important decision: should the journey continue in gaseous or liquid form? Because this results in two further important properties for the hydrogen infrastructure: temperature resistance and antistatic properties. As a gas, the two are very reactive – and therefore, there must be no electrostatic charging or even sparks in the lines and tanks. Because plastics are generally more susceptible to this than metals such as steel or aluminum, our material experts are also working on the right compounds here, which are also lighter and more flexible in terms of pipe routing.
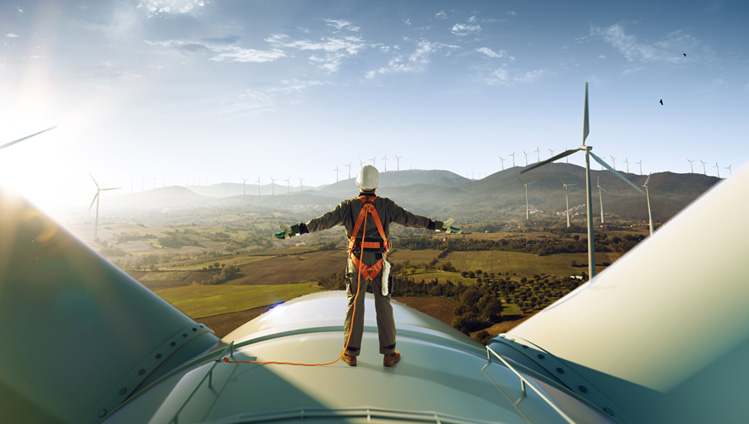
Safer than in gas form is further transported as a liquid, but this poses new challenges for the system. For this, our H2 pair must be cooled down to -253 degrees Celsius, and the materials used must be temperature-resistant accordingly. Once inside the vehicle they get very warm, because the ambient temperature here can easily reach +100 degrees Celsius and more. This is the temperature range we are dealing with when we are working on the right mixture for hydrogen transport. But it doesn't always have to be quite so cold: H2 can also be transported as an energy source in the form of ammonia, the compound of hydrogen and nitrogen; but for this it only requires the lines to withstand temperatures of -30 to +50 degrees Celsius. Solutions for ammonia transport are already part of Continental's product range.
Our team of two reaches an important stage on its journey at the gas station. Where, the pair must not get lost under any circumstances. And that's not so easy, because at 0.000000031 mm, H
2 is the smallest molecule with the lowest density – about 14.4 times less than the ambient air. This means that conventional tank hoses made of rubber or silicone would quickly cause our two hydrogen travelers to evaporate. And that would not only be a waste, but also dangerous at such a neuralgic point – a small spark could lead to an explosion.
So, all media-carrying and connecting components, such as hose cores, tank nozzles and couplings, must be particularly impermeable. Steel fails despite a low permeation level because it is heavy and inflexible. Our material experts therefore see the solution for this application situation in high-performance plastics, so that they can safely and flexibly guide our two hydrogen atoms on their way into the vehicle.
Hydrogen is clean energy for commercial vehicles
Now, we have almost reached the destination of our hydrogen journey, the fuel cell in the hydrogen-powered commercial vehicle. This is where our two companions are supposed to separate again after a long journey together. But only if nothing else interferes – for example, other molecules that they could pick up on their journey. So, cleanliness for the hydrogen infrastructure is another target our engineers are striving for.
This is because the chemicals leached from lines and transported onward can contaminate the proton exchange membrane in the fuel cell, leading to performance impairments and premature wear. For this line infrastructure, Continental's portfolio includes many components that are already in use today, including EPDM hoses for stack cooling, high-purity air intake and hydrogen recirculation lines, and products for the exhaust system and coupling technology.
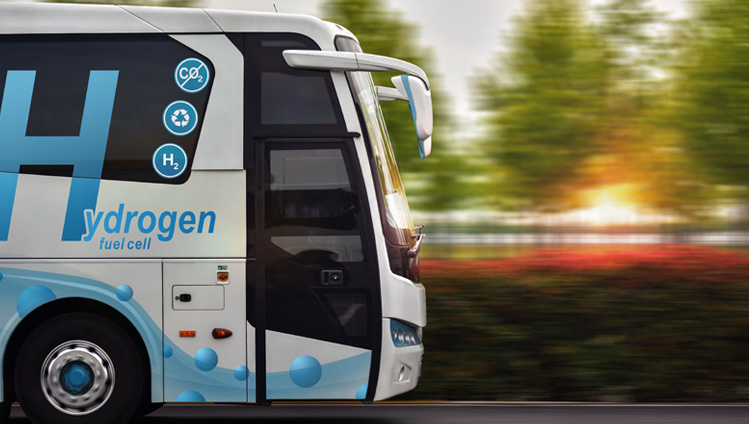
But when our hydrogen pair arrives cleanly in the fuel cell without any unwanted fellow travelers, they are made to react with oxygen under controlled conditions. The result is a lot of released energy that powers the vehicle. A little water, which is discharged to the outside via a pipe system. And most important no CO2, which could further fuel the climate crisis.
And this is precisely what makes fuel-cell technology particularly interesting for heavy-duty transport. which today accounts for around one third of CO2 emissions in the entire transport sector. But it is also of interest for other areas in which hydrogen could make zero-emission mobility possible in a user-friendly way. Namely, wherever weight, range and charging times play a major role. This also includes off-highway applications, for example, when construction and mining machines are sometimes operated 24 hours a day.
Our materials experts are working very hard to make this vision of the future a reality as quickly as possible. And then, perhaps in a few years, many, many hydrogen couples will be powering the latest low-loaders, excavators or loggers.
Challenges when Handling Hydrogen
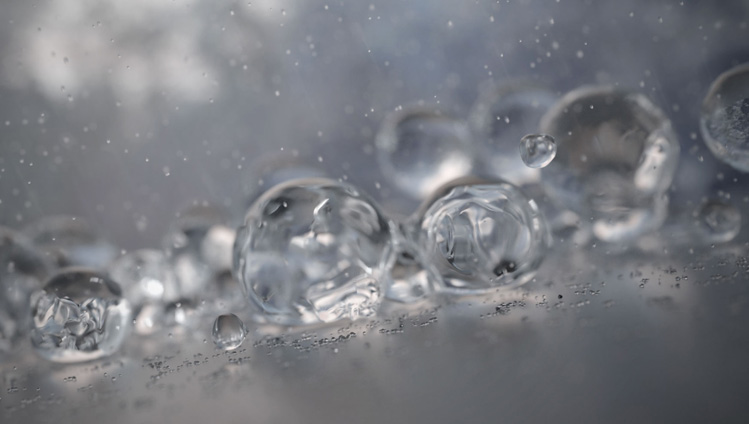
Impermeableness
As the smallest molecule with the lowest density, H
2 is so light that it would quickly permeate through conventional lines made of rubber or silicone. Therefore, all media-carrying and connecting components must be particularly impermeable.

Pressure resistance
Depending on the application situation, hydrogen is transported at up to 700 bar. For example, higher pressure shortens the time needed to refuel a vehicle. Components made of thermoplastics and elastomers must therefore be highly resistant to pressure.
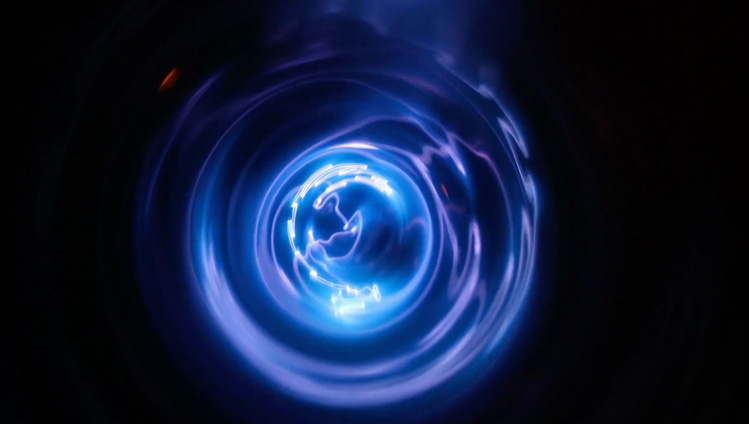
Antistatic
Hydrogen is a hyper-active and flammable gas, a certain air ratio could lead to an explosion if an electrostatic charge or a small spark occurs. Plastics are generally more susceptible than steel or aluminum.

Temperature
Hydrogen becomes liquid at -253 degrees Celsius, whereas the temperature in the fuel cell vehicle can be +100 degrees Celsius and more. The materials used in lines must therefore be suitably temperature-resistant.
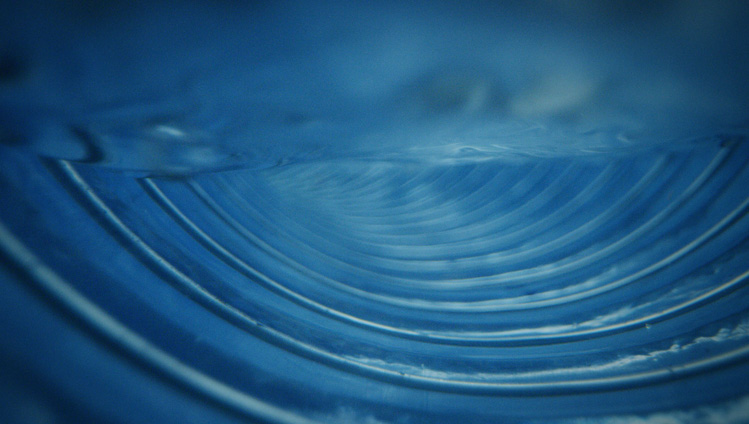
Cleanliness
Chemicals leached from H
2 lines and transported onwards can impair the performance of fuel cells and cause them to wear out prematurely. High-purity materials are therefore essential for lines and hoses.
Read more about which solutions our experts develop to tackle hydrogen challenges.