A Noruega é um país dos superlativos. Além de quase 240.000 ilhas1, 1.000 fiordes2, 2.000 cachoeiras3 e 200.000 alces4, lá também há muitos carros elétricos. Isso não é um milagre, mas uma estratégia: o país promove a eletromobilidade há 30 anos, porque a eletricidade verde costuma ser mais barata que a gasolina ou o diesel na Escandinávia. Os herdeiros dos vikings também têm as maiores ambições para o prazo de mudança: até no máximo em 2025, não devem mais ser vendidos novos carros de passeio e veículos comerciais leves com motores de combustão. As condições são, portanto, perfeitas à transformação para uma mobilidade sustentável e de baixas emissões.
É sério? De fato, as condições climáticas em um país onde há até onze metros de neve no inverno e temperaturas tão baixas quanto -40 graus Celsius não são nada ideais para a tecnologia de mobilidade elétrica. Para que a bateria altamente sensível ainda possa manter seu desempenho total – independentemente de estar fria ou quente – nossos engenheiros precisam repensar completamente o gerenciamento de temperatura no veículo.
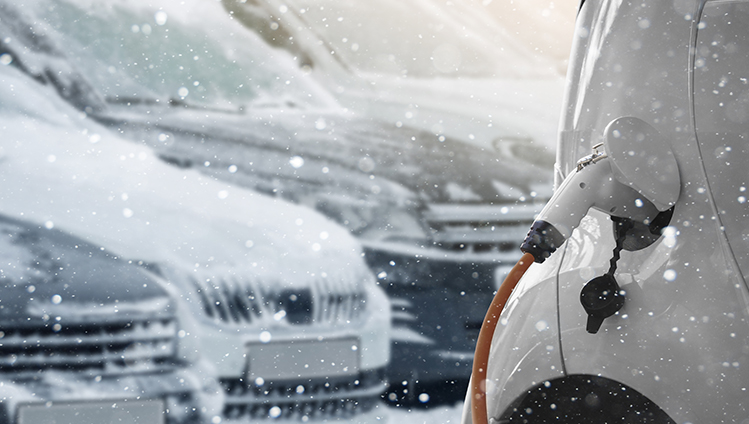
Frio na mobilidade elétrica? Não, obrigado!
Quem já foi esquiar sabe que as baterias recarregáveis são sensíveis. Isso se aplica a baterias em smartphones, bem como em pedelecs (bicicletas elétricas) ou veículos elétricos. Elas simplesmente não se sentem bem, seja no calor do verão, no frio do inverno e em condições extremas. Temperaturas frias, em particular, retardam os processos eletroquímicos, a tensão da bateria cai e existe o risco de descarga profunda, o que é prejudicial para a bateria. O problema: a energia elétrica perdida devido à temperatura errada não pode mais ser recuperada. É por isso que o desempenho de uma bateria de veículo elétrico é mais alto em um corredor de temperatura entre 15 e 40 graus Celsius. E é exatamente por isso que nossos sistemas de condutores têm um impacto direto no alcance de carros elétricos.
Um condutor (de resfriamento) bem longo
Basicamente, a fabricação de veículos elétricos é significativamente menos complexa do que a de veículos com motores a combustão: um motor a gasolina com câmbio manual, por exemplo, tem cerca de 1.400 peças, enquanto um carro elétrico precisa de apenas 200 componentes individuais. Exceção: condutores de resfriamento e aquecimento. Porque enquanto no motor de combustão apenas o motor em si precisa ser resfriado e o calor gerado pode ser usado para o aquecimento da cabine, o sistema de condutor no veículo elétrico é obviamente mais complicado. Aqui a temperatura tem que ser gerenciada para vários circuitos, para o powertrain, o ar condicionado e, por fim, a bateria.
Dependendo da temperatura externa, a bateria precisa de resfriamento ou aquecimento. Como regra, para isso hoje são usados sistemas separados, que são conectados por um permutador de calor. E assim o comprimento total do condutor em comparação com o motor de combustão é duplicado para quase 30 metros. O mesmo se aplica ao número de conexões de encaixe, acoplamentos de liberação rápida e grampos necessários. Em um grande veículo comercial, isso pode totalizar quase 100 tubos e mangueiras individuais, além de muitos elementos de transição.
O mais importante é estar estanque
A propriedade mais importante para condutores em veículos elétricos: estanqueidade absoluta. Porque uma mistura de água e um fluido de resfriamento, como glicol, flui através dos tubos e mangueiras. Portanto, os materiais utilizados também devem possuir a resistência química adequada. No passado, eram usados materiais EPDM para mangueiras flexíveis, enquanto alumínio ou aço eram usados para tubos mais estáveis. Hoje, as misturas de borracha reticulada com peróxido estão cada vez mais sendo substituídas por elastômeros termoplásticos, alumínio e aço estão sendo substituídos por plásticos PA, PP ou PPS. Dependendo dos requisitos do OEM, esses materiais também podem ser combinados entre si e conectados por meio de conectores apropriados para a solução ideal.
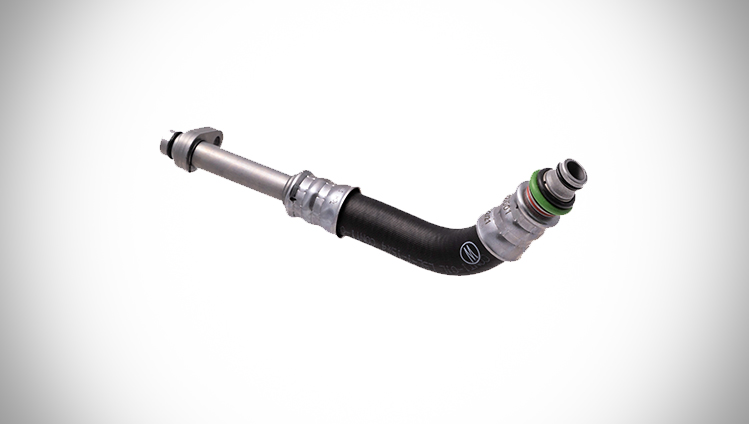
Aliás, ao cooperar com os fabricantes, de fato são necessárias diferentes expertises. Os OEMs estabelecidos geralmente já têm ideias muito detalhadas e concretas sobre o projeto, de modo que é mais provável que o tempo seja investido no desenvolvimento e aprovação de diferentes opções de materiais. Nossos clientes corporativos iniciantes no setor de e-Mobility concedem com prazer aos nossos engenheiros e engenheiras mais liberdade de design e, na seleção de materiais para mangueiras, tubos e similares, confiam em nossos muitos anos de know-how.
Sustentabilidade + mobilidade elétrica = futuro
Como sempre na mobilidade elétrica, o tema da sustentabilidade também tem um papel importante no material. E não apenas porque os consumidores finais estão valorizando cada vez mais a conservação de recursos e produtos duradouros. Felizmente, os condutores de um veículo geralmente são projetados de tal forma, que não precisem ser substituídos. Isso por si só já reduz o consumo de recursos. Além disso, nossos desenvolvedores e desenvolvedoras prestam atenção especial no peso dos componentes. Porque devido ao alto peso da bateria, cada grama possível deve ser economizada em outro lugar. Graças aos novos materiais, que são tão estáveis e estanques quanto seus antecessores que, apesar de sua espessura de parede reduzida, quando realizamos uma comparação já conseguimos economizar mais de 50% em peso.
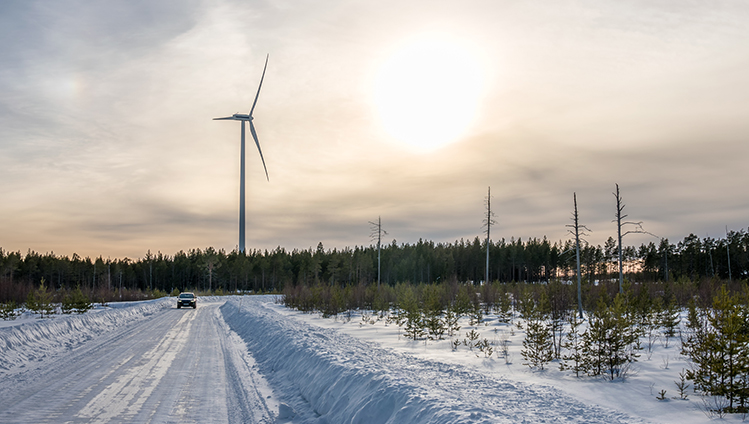
A sustentabilidade também é a chave na produção própria da Continental. Queremos neutralizar nossa carga de CO2 em todo o mundo por meio de emissões negativas – incluindo na produção, na cadeia de suprimentos e no fim da fase de uso. Nosso foco está nos veículos sem emissões de propulsão. E isso não é um desafio pequeno. Porque a maioria dos condutores e mangueiras, sejam EPDM, TPE ou outros plásticos, não consistem apenas em uma única camada, sendo bem difícil separar o reforço integrado de outras camadas. No entanto, as chamadas monocamadas são bastante cogitáveis. Grânulos reciclados, por exemplo, de garrafas PET antigas, também podem ser utilizados. Nossos especialistas em materiais ainda veem muito potencial inexplorado aqui. E é aqui que o círculo se fecha: a verde Noruega também leva muito a sério suas obrigações de reciclagem – a primeira usina de reciclagem de baterias de carros elétricos está agendada para começar a operar em Fredrikstad muito em breve.
1https://www.laenderdaten.info/inseln-nach-land
2https://www.visitnorway.com/things-to-do/nature-attractions/fjords/the-fjords-explained/
3https://www.worldwaterfalldatabase.com/country/Norway/list
4https://www.nordlandblog.de/elche-norwegen-beobachtung-safari/